End of life
When the hardware for the automation system you’ve deployed throughout your entire installed base is suddenly declared end-of-life, you’re faced with a problem.
That’s what happened to Apex Energy LLC. A natural gas exploration and production company, Apex is headquartered just outside Pittsburgh, Pennsylvania. Working with midstream gas companies and gas utilities, they invest in unconventional oil and gas properties in the Appalachian Basin, with a focus on proven Marcellus and Utica horizontal well development.
As a longtime customer of systems integrator Strata Innovative Solutions (formerly Flow Data), Apex had used Strata’s field-proven PadPro automation solution starting with their second drilling site, or well pad. They were happy with the solution. But in 2019-2020, manufacturers of the hardware components began to end-of-life their products. For their planned growth, Apex needed a new solution that would offer as seamless a transition as possible.
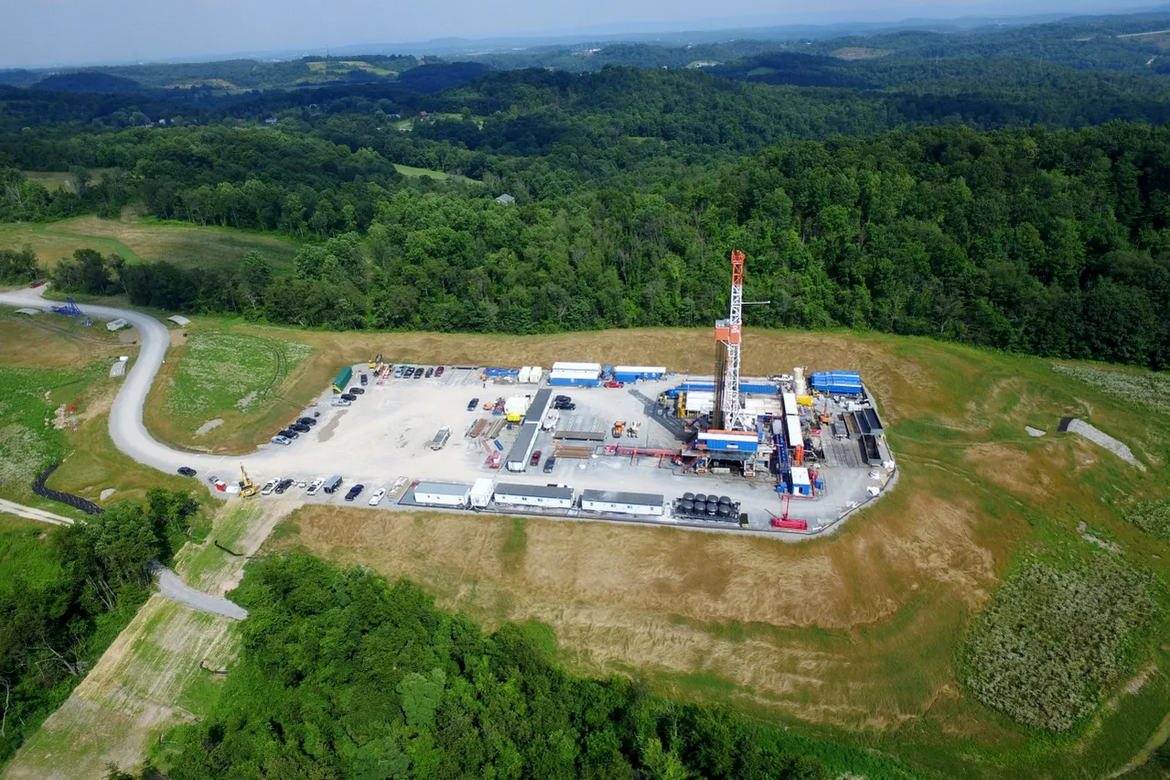
An Apex well pad
Hardware choices
Coincidentally, Strata was running into memory and processor speed limitations in the current hardware, and they needed to find a more capable system to automate well pads for all their customers. A systems integrator primarily for upstream and midstream Oil and Gas, Strata also handles renewables, manufacturing and supply chain, and utilities. They have a breadth and depth of knowledge and experience, especially in the O&G industry, and offer a one-stop-shop solution with electricians, panel shop, automation technicians, and engineers.
Ninety-five percent or more of all upstream O&G well pads are automated, notes Richard Best, Strata’s Eastern Region Operations Manager. “Generally, a company standardizes on a solution—programming, hardware, etc.—across a region. The solution selection is based on the requirements of the O&G play: whether it’s an oil field or a gas field, whether it’s wet or dry, the type of formation (Marcellus, Permian, etc.), the type of drilling used, and the company's operating practices.”
For years Strata’s proprietary C/C++ software PadPro provided monitoring, HMI, and control to well pad operators. PadPro ran on the Schneider® 300 series SCADAPack, which supported C/C++ programs and worked in conjunction with an Android HMI with PostgreSQL database. But now the Schneider hardware was no longer available, and Strata looked for a replacement.
“We evaluated other controllers, but the Opto 22 groov EPIC® system won by a long shot, based on capabilities, availability, and pricing,” says Richard. “Also, our Product Development team recommended Opto.”
Strata was already familiar with Opto 22. “We have actually been using Opto 22 platforms on Oil and Gas projects dating back to the late ‘90s, several of which were international projects,” notes Paul Brennan, a founding member of Strata. “With the release of the EPIC system, the Opto 22 became an even stronger candidate for Oil and Gas solutions.”
In 2021 Strata decided to migrate their solution to the Opto 22 platform, for several reasons:
- Linux OS
- Competitive price
- Robust memory and processor
- Numerous I/O (much more than an RTU)
- Multiple protocols and programming techniques
- UL Hazardous Area Class 1 Div 2 rating
- Wide -20 to 70 °C operating temperature
StrataVu software
As they chose groov EPIC, Strata also revised their PadPro application to match the new hardware capabilities, releasing it under the name StrataVu.
Tailored to upstream O&G, StrataVu solves multiple problems for operators in the industry with a collection of pre-built modules that handle well pad-related tasks. Customers choose and configure the StrataVu modules they need. This modularity lets customers choose functions specific to the tasks they’re trying to perform.
“A good example is the Cause & Effects module,” says Keith Thomson, StrataVu lead development engineer. “It’s a simple way for a nonprogrammer to create a familiar event-driven system that acts on events for site and process safety. A technician just fills in a web-based chart of inputs & outputs. It’s a no-code approach, configured rather than programmed, with standardized pieces so you can build out more easily.”
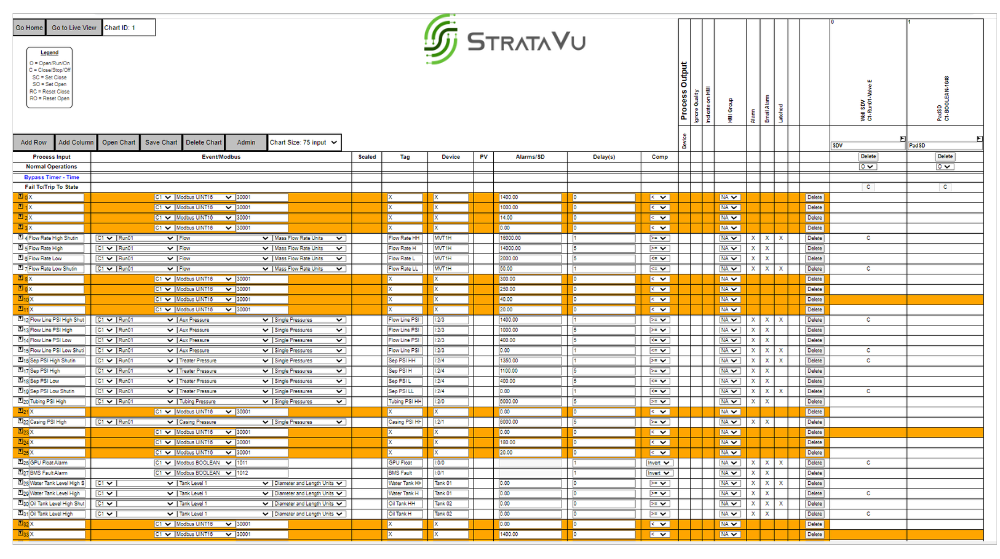
StrataVu’s Cause & Effects module: This configuration interface lets customers easily configure an event-driven system.
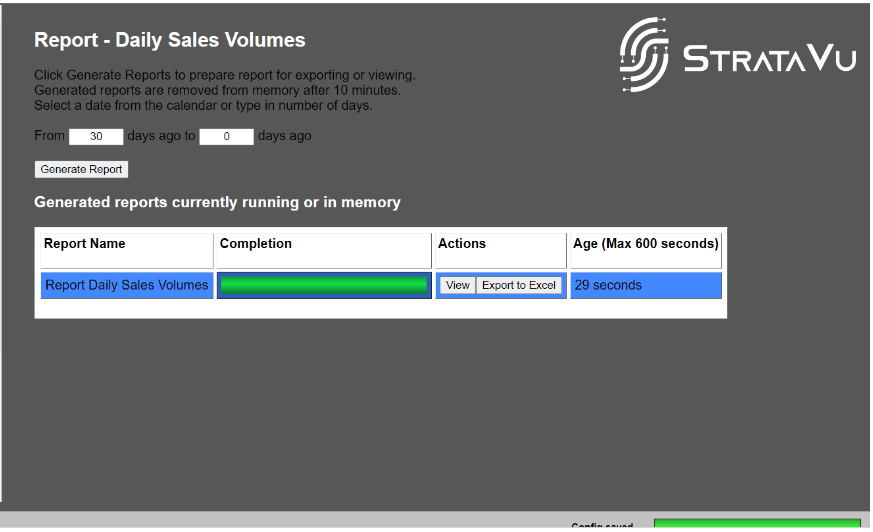
StrataVu’s daily volume report for business use
Strata uses Secure Shell access (SSH) to load StrataVu on the EPIC’s Linux operating system, where it runs. Typically StrataVu handles 90% of control and data acquisition, but perhaps 10% may be customized using CODESYS for IEE 61131-3 compliant languages, Node-RED, or Opto 22’s PAC Control programming on the EPIC. Reports and trending data for operations are in StrataVu’s web interface, and customers can add items to a database historian for long-term storage.
System architecture
Apex uses a distributed architecture for their well pads. Each well pad has two wells running through a Gas Production Unit (GPU) with a pad control panel on the GPU. They find this architecture is more easily expandable than a centralized architecture. It also reduces points of failure and saves on wire and conduit.